UV Curing: What To Know
What is UV Curing?
UV Curing is a special curing process that utilizes UV lamps to create a chemical reaction or physical action that takes place, resulting in a harder, tougher or more stable linkage or substance.
In recent decades, UV curing technology has grown rapidly. The instant curing technology that revolutionized printing has now spread to other industries and technologies due to its ability to be processed and packaged within seconds of exposure.
How does UV Curing work?
UV curing is a photochemical process that instantly cures inks, coatings, or adhesives using UltraViolet light. Liquid monomers and oligomers are mixed with a small percentage of photoinitiators and then exposed to UV energy. After a few seconds, the formulation hardens or cures, ready for further processing.
Want to learn more about how UV curing can assist your business?
Call us at 860-677-6400 or fill out a form
Some advantages to UV Curing include:
- Processes can be completed within seconds.
- Automated processes are easy to set up.
- An all-in-one system with less waste generation.
- No solvents are needed; 100% cures without any other materials.
- Simplified system handling.
- Minimal costs are involved.
What are UV inks used for?
The UV curing process can be used to cure UV inks, adhesives, and resins. One of the greatest advantages of UV inks is that they stay liquid as long as they are not exposed to UV light and cure almost immediately, allowing greater freedom for the operator. For printers with consistent orders and a desire to increase production throughput, UV inks are an excellent choice.
Adhesives and sealants are formatted in either epoxy or acrylate forms. Applications using plastics, rubbers, glass, metal and ceramics rely on adhesives and sealants. Adhesives offer bonding that is not visible. Sealants cure and form in place. Conformal coatings (layer of protection for circuit boards) and encapsulants (electrical insulation) are applications that typically use UV curing.
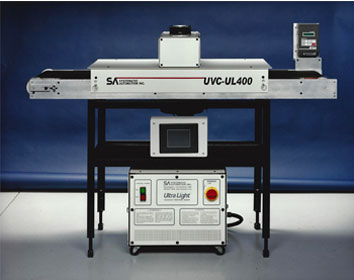
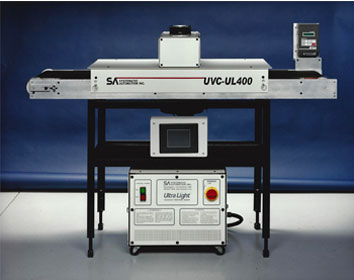
Pictured: UVC UL400
We rely on UV inks, coatings and adhesives for a number of reasons, including:
- UV substrates do not contain solvents and volatile organic compounds (conventional substrates have 40%)
- They prevent drying/sticking to printers overnight
- They are space efficient, with a low starting/cleaning time
- Traditional solvent-based inks take a long time to dry; curing with UV is instant
- UV lamps are more energy efficient than heaters/driers
- They give an improved quality of ink/polymer/resin substrate and cure
- Unlike solvent-based inks, UV inks cure instantly and remain fluid until exposed to UV light
- Inks that are cured with ultraviolet light are generally ready to pack for customers almost immediately after they are finished curing
- UV inks are optimal for consistent throughput when printing multicolor designs (in large quantities)
NOTE: If left out, the UV from your factory lights can partially dry the ink. For UV ink printers, we recommend covering the machine so no light can pass through if you wish to leave the ink on the screen overnight or over a break.
When to Pretreat
The UV inks are not as resilient as the solvent based inks. In the event the product will be used repeatedly, Systematic Automation heavily recommends pretreatment, which can range from flame, plasma and Fierosil. To determine if you need to pretreat an item, you can conduct a dyne test or a cross scratch test.
Cross Scratch Test: A cross scratch test is simple, and only requires a blade. You will know an image will not stand the test of time if a blade is pressed against it and scratches it off. You might even be able to remove the ink using your fingernail.
Dyne Test: You will need a dyne kit with droppers in order to perform this test. With the test you will be able to determine if you have a good dyne level if the liquid maintains its state. If your dyne level is less than optimal, liquid will bead out and not leave the full liquid line on your cup.
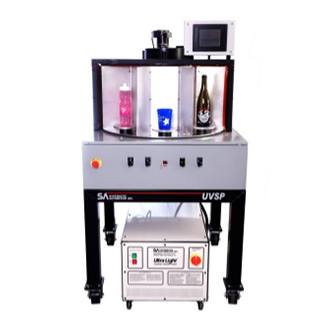
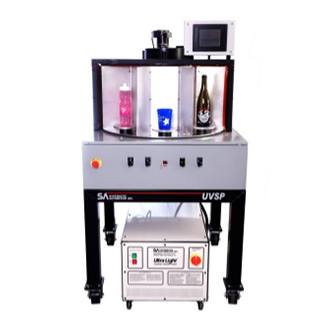
Pictured: USVP
Which UV systems will give you the optimal result for your UV process?
UV LAMPS
Traditionally, UV curing is done using lamps that cover a wide spectrum of wavelengths. This UV system comes with a series of advantages that make it the ideal choice amongst operators, such as:
- There are a number of options for inks, adhesives, and more.
- There is a blower on each Systematic Automation conveyor that not only exhausts the ambient heat, but also has a duct connection so you can exhaust the ozone from the lamp outside of the building.
- A UV lamp has a life expectancy of approximately ten years or 800 hours.
- Using UV lamps for curing gives you much more flexibility in controlling distance between product and lamp than using LEDs.
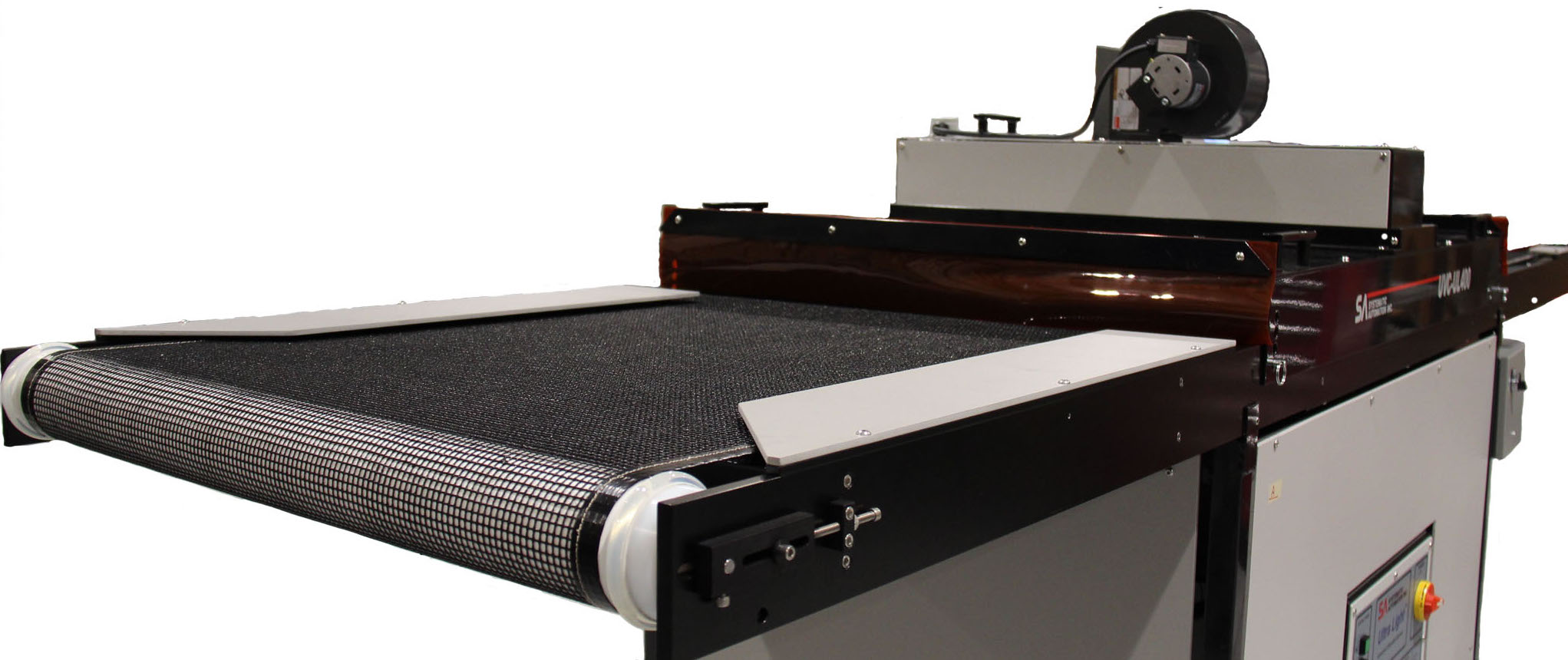
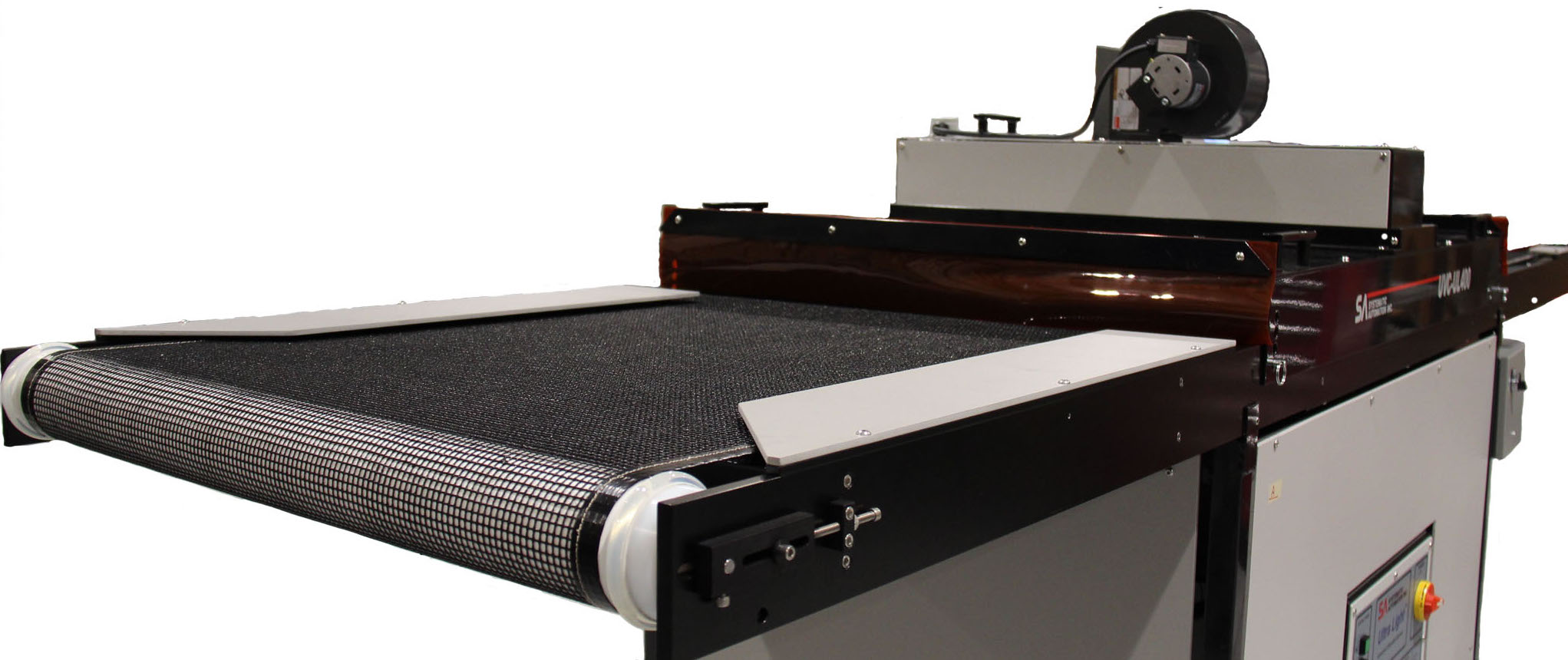
Pictured: UV Conveyor
LED LAMPS
There is still work to be done on the technology that will enable UV LEDs to be widely used in the UV curing industry, but even today operators can see benefits in using LED over traditional UV lamps because:
- You get a greater return of investment from LEDs.
- LEDs do not require consumable lamps.
- LEDs typically last over 60,000 hours which is the equivalent to 750 standard UV lamps.
- There is no need to exhaust emissions.
- Ease of handling; LED lamps are compact and lightweight.
- A LED lamp emits a single wavelength that is only 395 nm.
Systematic Automation offers UV curing solutions for your application and budget. Contact us to learn more about the best options for your business.
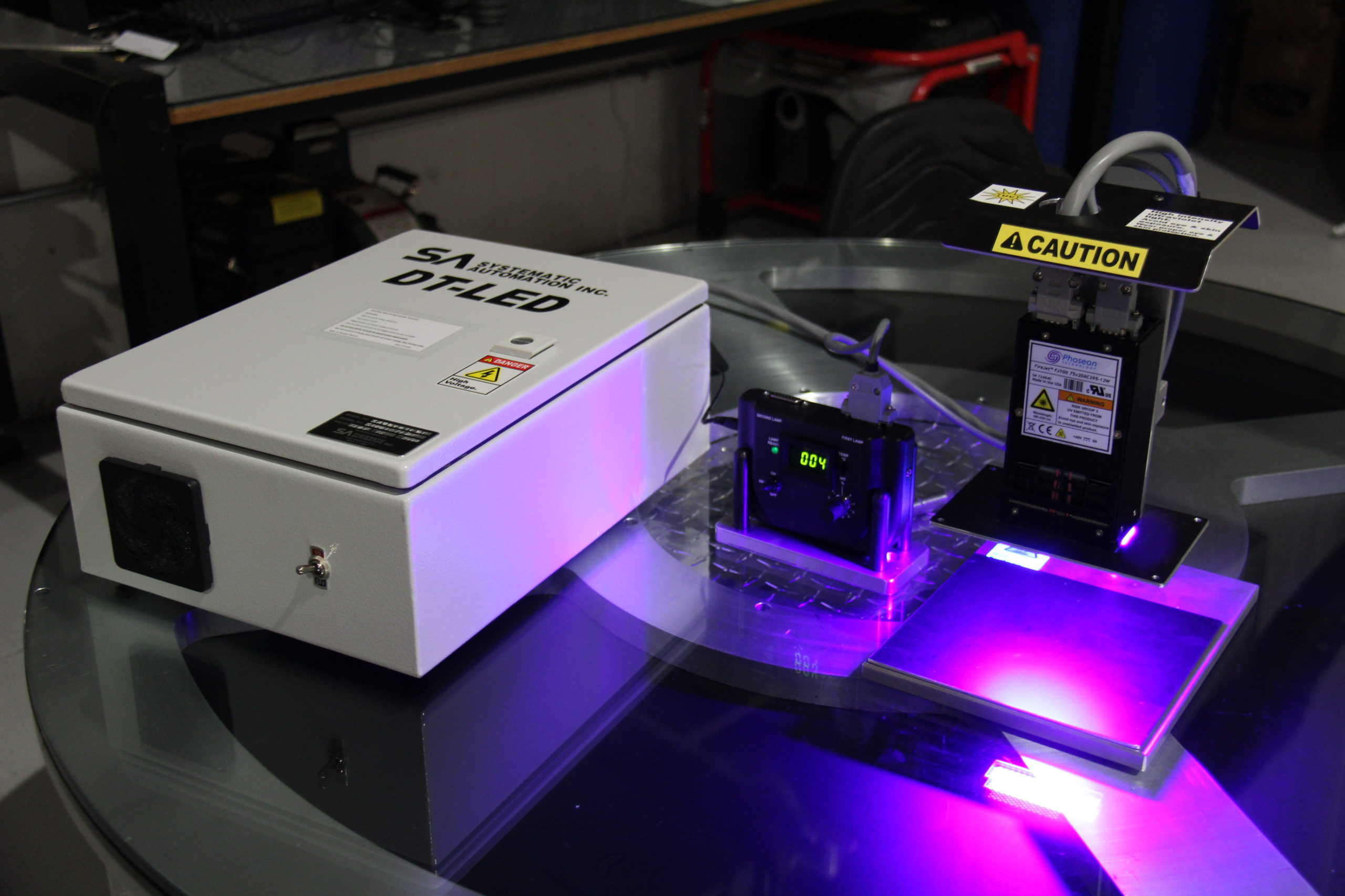
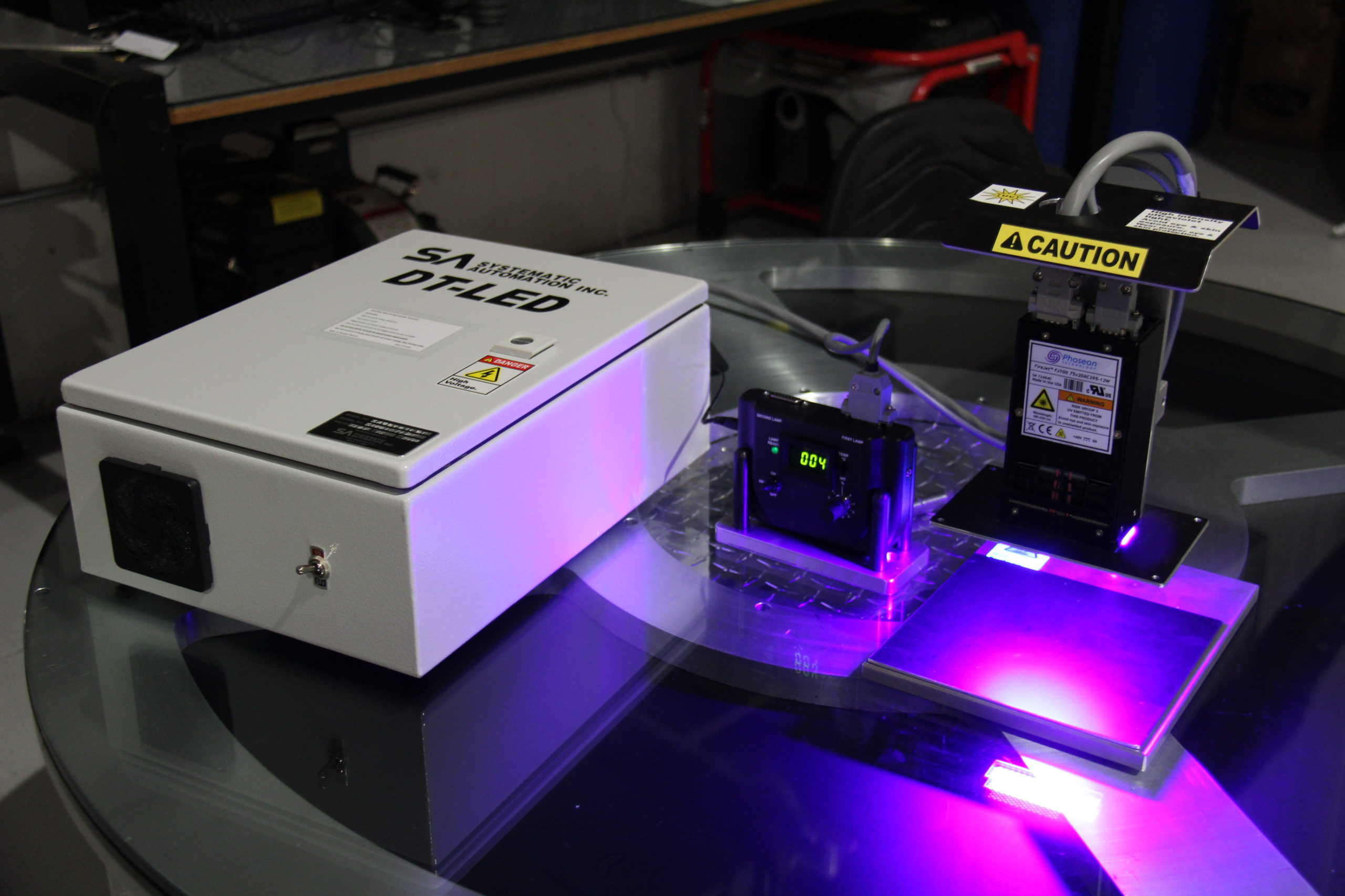
Pictured: DT-LED
H (mercury vapor) lamp vs. a D (iron) lamp
An iron lamp will significantly increase intensity. Nanometer ranges are available on our website under UV and lamps. Iron spikes in the 395 nm range. Gallium additive is also available with a peak in the 410 nm range. Your ink supplier will verify if this will be more effective. If so, we recommend you try out an iron lamp and raise the lamp an inch or more. By raising it, you will allow more of the light emanating from the center of the lamp to reach to outside of the material being printed. Iron lamps and additive lamps in our experience are harder to start (they may need to be fully cool to start and may require more than one attempt). They also have a shorter life.
Lamp Maintenance
Wait for lamps to cool before restarting. When a lamp is turned off, ions and electrons recombine and charge carriers are lost. In contrast, when the lamp is still hot, the atoms in the lamp move quickly and this leads to a high resistance when the lamp is restarted.
Keeping your UV lamp clean can help prevent problems like devitrification that can occur when it becomes overheated after surface contamination. Natural "devitrification" occurs when quartz converts back into a crystalline structure, which is a very poor UV transmitter. As a result of devitrification, quartz becomes less transparent to UV light, with many white spots on the surface. Once this occurs the lamp will become very poor at transmitting UV. The different density causes micro cracks in the body of the lamp and loss of vacuum power, which will lead to lamp failure. UV lamps may need to be replaced once devitrification begins.
A UV lamp can also undergo devitrification if chemical impurities on its body, such as oil secreted by the skin, catalyze the process. Our recommendation is:
- Handle lamps with gloves
- Use an alcohol wipe to clean the lamp body before use, such as isopropanol alcohol
Replacing a Lamp and Reflectors
99% of failures are misdiagnosed as lamp failures. Most often, these are actually failures caused by other components such as capacitors, ballasts, reflectors, or ignitors. However, there are some standard signs that will alert you when a lamp replacement is necessary. There are two issues that will demand immediate replacement: a lamp with depleted running voltage, and a lamp that is swollen.
Low Voltage: A lamp's running voltage will decrease over time. When the lamp voltage drops below the recommendation set by the Voltage Relay, the lamp will not send a "Lamp ready" signal to the press. If this happens, change your light immediately.
Reflectors are extremely important, generating around 70% of the usable UV, so they should be checked and maintained regularly. Reflectors should be replaced whenever the lamp is changed, or sooner if they are dirty or damaged.
What are the advantages and disadvantages of an electronic power supply?
Advantages:
- Energy savings due to better efficiency
- Lighter and smaller size for better handling
- Stepless voltage and power switching in an instant
- Extended lamp life
Disadvantages:
- Shorter life-span
- More heat sensitive — requires cooling
Working Safely with Ultraviolet Radiation
Ultraviolet Radiation
Ultraviolet radiation can be dangerous to the eyes and skin of personnel. Adequate shielding blocking UV light exposure must be provided. If unsafe levels of light are allowed to escape during operation, all personnel in the vicinity of the system should be required to wear goggles with UV certified lenses. Protection is needed for indirect as well as direct eye exposure. Discomfort from excessive eye exposure to ultraviolet light typically occurs about six hours after exposure. Personnel who experience eye pain after possible exposure to direct rays from the UV lamp should see a doctor. Furthermore, in the event that adequate shielding is not possible, all personnel within ten feet of the lamp should wear gloves and a long-sleeved shirt to protect their hands and arms.
There are no present U.S. Government standards on worker exposure to ultraviolet light. However, there is a NIOSH document, “Criteria for a recommended standard… Occupational Exposure to Ultraviolet Radiation” (No. HSM 73-11009), and several useful publications are available from the Bureau of Radiation of the Food and Drug Administration.
Ozone
Ozone is a gaseous form of oxygen which is formed by ultraviolet light generated from arc type UV lamps (not LED lamps which generate no ozone). It’s characteristic odor is readily detectable at low concentrations (0.02 to .05 parts per million). Excessive exposure to ozone produces local irritation of the eyes and of the respiratory tract. It can be dangerous at higher than acceptable levels in the workplace. Be sure your equipment has adequate ventilation. Do not use your equipment in a confined space. Maintain work area ozone levels below the OSHA permissible exposure limits of 0.1 part of ozone per million (ppm) of air in an 8-hour time weighted average. Maintain a healthy work area by monitoring ozone levels using detecting instruments such as the EZ-1X device available from Ozone Solutions.
Click here for a material safety data sheet (MSDS) on ozone. Contact your State OSHA office for compliance assistance. Contact Systematic Automation service department (860) 677-6400 ext.117 for assistance on how to provide adequate ventilation for your particular machine model. Ozone free lamps are available from Systematic Automation. These type of lamps may not be appropriate for your particular application. Call our service department for information on ozone free lamps.
Temperature
Surface temperature of the lamp during normal operation will exceed 800 degrees Fahrenheit. Before attempting service procedures on the lamp, allow the unit to cool. Observe appropriate precautions to avoid burns. Handle the bulb with cotton or surgical gloves or a lint-free towel at all times, as fingerprints can be etched into the quartz.
High Voltage
Insulated electrical cables carry high power from the power supply to the lamp. These voltages can be dangerous. Precautions should be taken in both the location and protection of these lines.
A high quality cable, rated at 20 KVA, is used in all high voltage cables manufactured by Systematic Automation and can be supplied to users for any additional connections that may be required.
SOME OF OUR SATISFIED CUSTOMERS