Screen printing on glass tubes
Screen printing on your glass tubes can be a tricky process if you are printing in a high production capacity. Automatic screen printing machinery for glass tubes is less common than many other applications. High production requires an attention to detail on the prints and measures out in place in order to reduce chipping of the glass when fed through an automatic loader and moved through the machine, which would result in loss of product.
The Model PEN Printer has been optimized to print on glass tubes. All that is needed is a single operator to load the PEN Printer automatic feeder. The PEN Printer will do the rest, from sorting the loaded glass tubes to printing them to curing them with your preferred means of curing. All manufacturing and engineering is done in house at Systematic Automation located in Farmington, CT. We are available to work with you on automating your application.
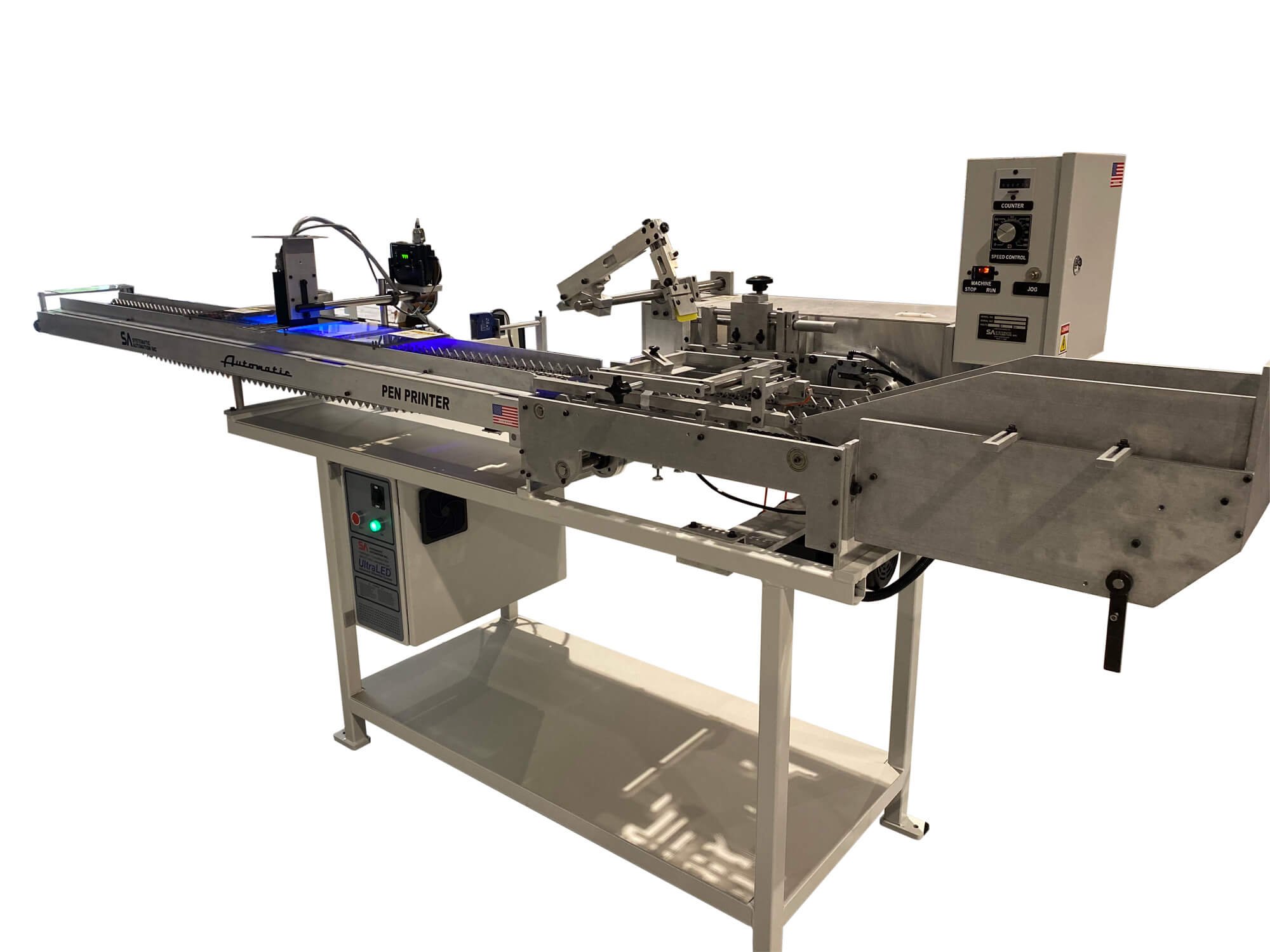
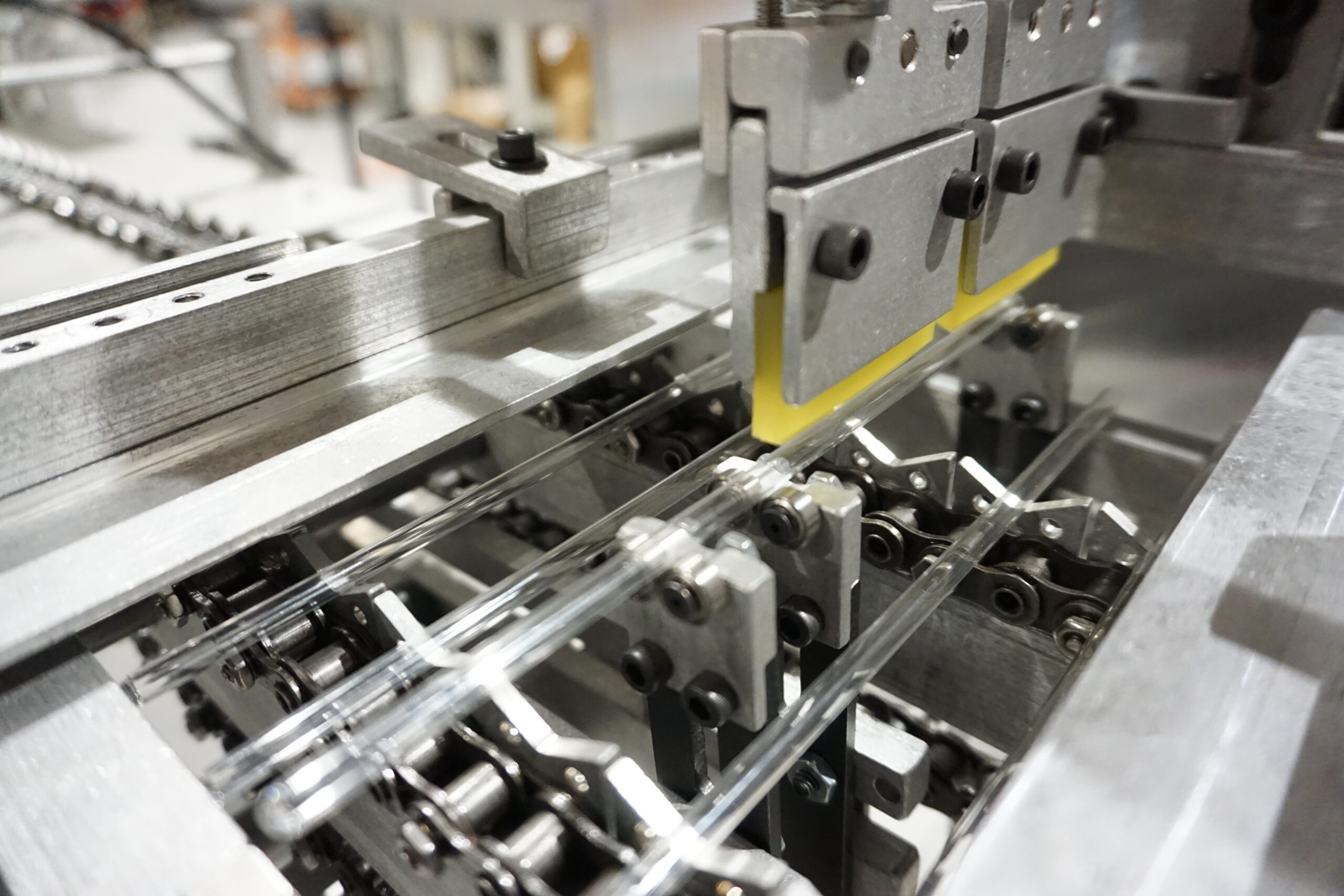

Automate your glass tube printing
The Model PEN Printer is the industry standard for automatically printing on your glass tubes. The PEN Printer excels at high speed production that can reach up to 4,200 parts per hour. Machine features simple analog controls for user simplicity. Different curing options can be integrated such as conventional UV, LED or a dryer oven. The dryer oven is most popular with glass applications because solvent based inks (cured through oven) feature optimal ink adhesion. Flame treatment or Fierosil for your glass parts may also be integrated if you want to use a pretreatment for UV curing. You may have glass tubes that vary slightly in diameter. The PEN Printer indexing chain can be made to fit an array of your different sized tubes. The cradle that transfers the glass tube up to the print station can be changed for different sized glass tubes.
The PEN Printer features a mechanical design for simple upkeep and troubleshooting. All machined components are made at the SA factory in Farmington, CT. The simplicity of the design also ensures the machine will not only be reliable but will last decades of consistent high production use. SA technicians are on standby for immediate assistance in case you require on-call or remote video time.